In injection molding technology, the mold is usually the weakest link in the entire process.
It is estimated that 75% of defects found in injection molded parts are related to mold design and errors made at the design stage of a given element. Adjustments to a mold already at the stage of its production are very expensive and sometimes impossible to implement without a complete change of the design concept.
By performing “virtual tests”, without the need to build physical models, we help our clients make a conscious choice of the most optimal solutions for each analyzed part, both in terms of processing parameters and mold design.
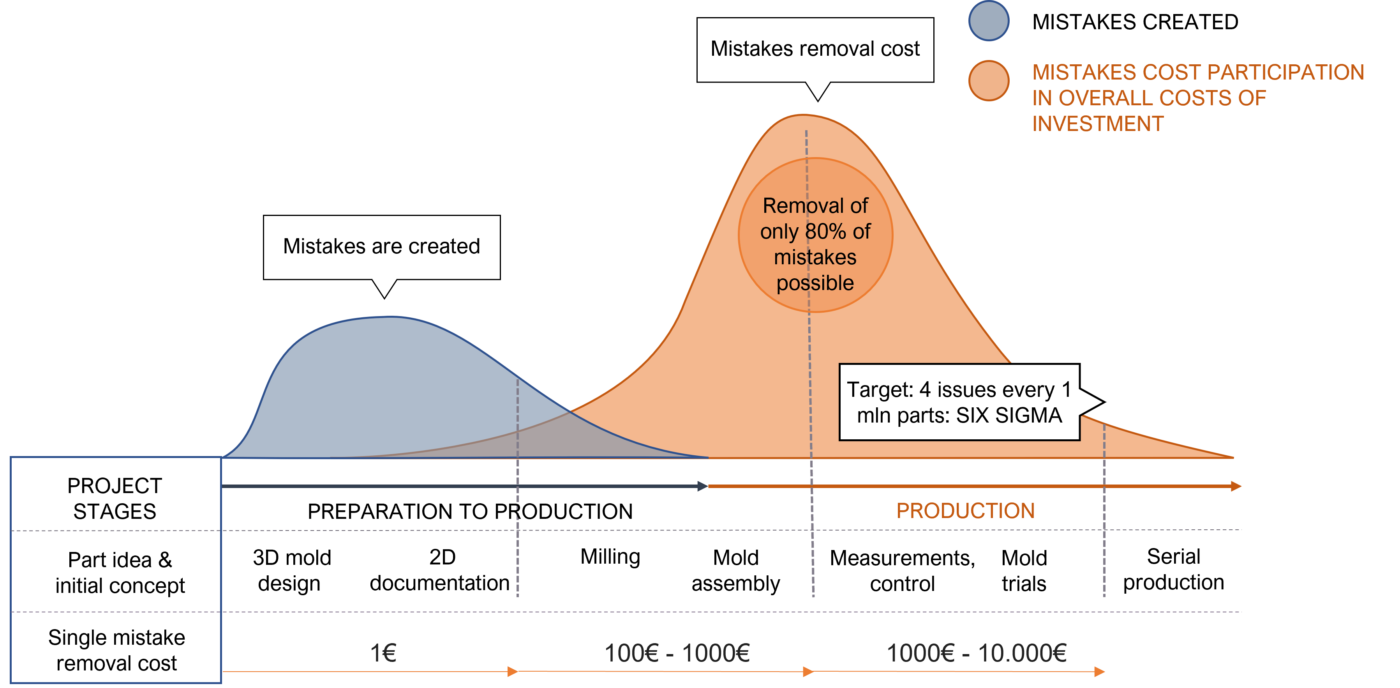
Why work with us?
Molds design and the processing of plastics are complex issues in which many interrelated factors add to the end result. Incorrect pricing usually ends with the client’s decision to implement the project in a different production plant. On the other hand, underestimating the cost of the project may lead to lower profitability of the entire business. Errors and omissions in the initial stages of the project implementation usually come to the surface during first mold trials, and the costs of their elimination are very high. That is why it is so important to properly analyze and simulate the part before the tool is manufactured.
Buying your own simulation software is not always profitable
Purchasing simulation software in the subscription model is a cost of several or even tens of thousands of euros per year. It is a considerable investment that can only pay off in the case of the implementation and implementation of several dozen projects.
The software itself is just the beginning
We must remember that the simulation tool remains only a tool, and in order to create added value, an experienced specialist who will be able to correctly interpret the obtained data is crucial to take full advantage of software’s potential.
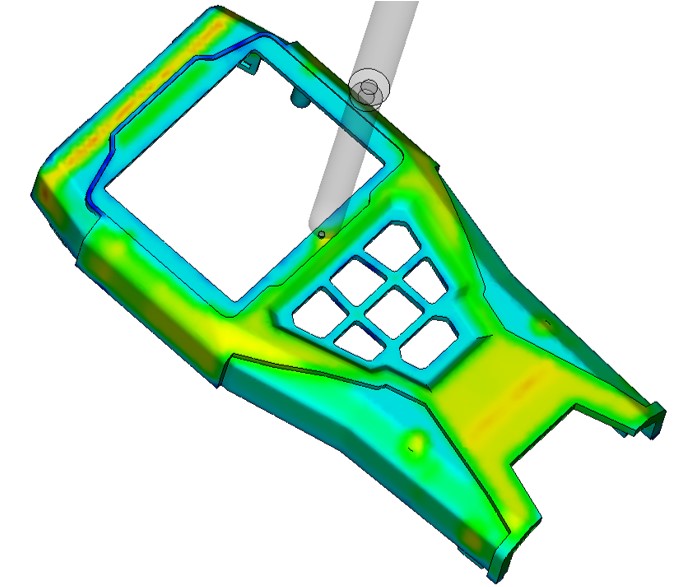
01
More than 20 years of experience in injection molding
We have over 20 years of experience in production of molded parts for the electronics, lighting, automotive, household appliances as well as the packaging industries. Over the years, our team has successfully implemented over 1000 projects.
02
Comprehensive approach
We offer full support at all stages of project implementation, starting from material consultations, optimization of molding geometry in terms of processing and design of a mold, to launching production and selecting optimal process parameters.
03
We guarantee the success of your project
Working with us will allow you to achieve real control over the implemented projects in terms of cost and quality. We will help you properly set the processing window, guaranteeing process stability with the shortest possible cycle time, repeatability of production and the required quality.